Digital twins and their application in industry
By Antonio Manjavacas (ESI-UCLM graduate).
"The cufflinks are very practical. Always good to have a spare "
—Billie Burke
Imagine that you are part of the team in charge of the safety of a nuclear reactor. It is up to you to guarantee that the facility implements all the necessary safety measures to avoid accidents, both on the environment and on its workers. In order to achieve this objective, it would be interesting to estimate how the reactor's safety systems will react to different accidental situations that we cannot afford to replicate in a real way, given their danger. We need a way to virtually simulate the behavior of the system in different potentially dangerous scenarios. And what better way to do it than through a digital twin.
The first notion of digital twin It has its origin in 2003, by the hand of Michael Grieves, a NASA researcher, who established the key concepts of this paradigm. However, it would be his partner John Vickers, in 2010, who would suggest the term digital twin (digital twin) to combine the ideas proposed by Grieves.
Un digital twin it is a virtual representation of a physical system capable of simulating its behavior in response to certain inputs or stimuli. Digital twins of buildings, vehicles, robots, cities and even people have been developed, proving their usefulness in countless fields and sectors.
However, for digital twins to be consistent with the replicated physical system, there needs to be continuous feedback in the form of data between them [1]. Going back to the initial example: if we can collect real-time data from all the sensors of the nuclear reactor, we will be able to create a kind of virtual representation of it, know its current situation, and even study its response to different simulated accidental situations.
The data flow between the physical and virtual systems does not necessarily have to be bidirectional: as long as the physical system provides enough information, we will be able to create and maintain a digital twin of it. However, the flow of data from the digital twin to the physical system is especially interesting, allowing it to improve its behavior, detect operating errors, or react in advance to various critical scenarios.
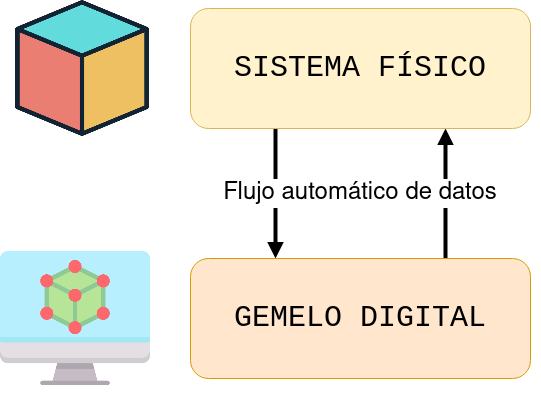
And it is that one of the main applications of digital twins is precisely to anticipate possible problems or exceptional situations that may occur in the simulated physical system. For example, in the Industry 4.0 sector, digital twins process data from devices or control systems to find out if they are about to fail, thus allowing different predictive maintenance strategies to be established [2].
We also find applications of digital twins in sectors such as the automotive industry [3], construction [4], energy industry [5], naval [6] or aerospace [7]. As can be seen, the benefits of digital twins in critical sectors are numerous, especially if we have high-value assets, the detriment of which can lead to significant costs and risks for people and organizations.
Digital twins also stand out for their potential integration with a large number of state-of-the-art technologies. Although it is advisable to be skeptical about the smoke that has been sold to us in recent years by different media and companies, it is true that artificial intelligence techniques, big data and properly integrated cloud computing are interesting in this field and increase the possibilities that digital twins offer.
For example, machine learning algorithms are excellent tools for value prediction, pattern analysis, or anomaly detection. Thus, using them together with digital twins could improve their ability to predict and respond to all kinds of scenarios. In turn, if these algorithms are capable of making decisions using huge volumes of data from physical systems, and we take advantage of the scalability offered by cloud computing to process said data, digital twins open the door to a future where worlds virtual and physical will soon be indistinguishable.
Bibliography
[1] Fuller, Aidan, et al. “Digital twin: Enabling technologies, challenges and open research.” IEEE Access 8 (2020): 108952-108971. [2] Aivaliotis, Panagiotis, Konstantinos Georgoulias, and George Chryssolouris. “The use of Digital Twin for predictive maintenance in manufacturing.” International Journal of Computer Integrated Manufacturing 32.11 (2019): 1067-1080. [3] Rajesh, PK, et al. “Digital twin of an automotive brake pad for predictive maintenance.” Computer Science procedures 165 (2019): 18-24. [4] Kaewunruen, Sakdirat, and Ningfang Xu. “Digital twin for sustainability evaluation of railway station buildings.” Frontiers in Built Environment 4 (2018): 77. [5] Botz, M., et al. “Structural health monitoring as a tool for smart maintenance of wind turbines.” Advances in Engineering Materials, Structures and Systems: Innovations, Mechanics and Applications. CRC Press, 2019. 1971-1975. [6] Fotland, Gaute, Cecilia Haskins, and Terje Rølvåg. “Trade study to select best alternative for cable and pulley simulation for cranes on offshore vessels.” Systems Engineering 23.2 (2020): 177-188. [7] Liu, Zhifeng, et al. “Data super-network fault prediction model and maintenance strategy for mechanical product based on digital twin.” IEEE Access 7 (2019): 177284-177296.